We all know how expensive and delicate concrete pumps are. This means that they have to be taken care of and they have to be serviced from time to time. The pumps have to be kept safely and used for the right purpose. One should also ensure that he or she buys only original concrete pumps and from reliable concrete trailer pumps manufacturers.
Below is a review of how to maintain concrete pumps and their spare parts.
1- Insulating the booms from time to time.
One should use a material that doesn’t absorb water to insulate the booms on the concrete pump. You can use neoprene to insulate your concrete pump machine. Neoprene is easily found in shops. So as to maintain the integrity of the concrete pumps paint, you should wrap your pump with saran wrap. In case money is a problem, you can also insulate only the last two parts of the pump. This is because of the fact that an empty concrete pump pipes freezes faster than a pipe that is full of concrete.
The frozen concrete layer normally peels of as soon as pumping begins. This creates a frozen slug of concrete which normally plugs on the users eyebrows. One should regularly check the atmospheric temperature and even the concretes temperature. The temperature of the concrete of the pumps fluctuates depending on the daily activities of the pump during the day. Heating the concrete before using it at the job site is also another option.
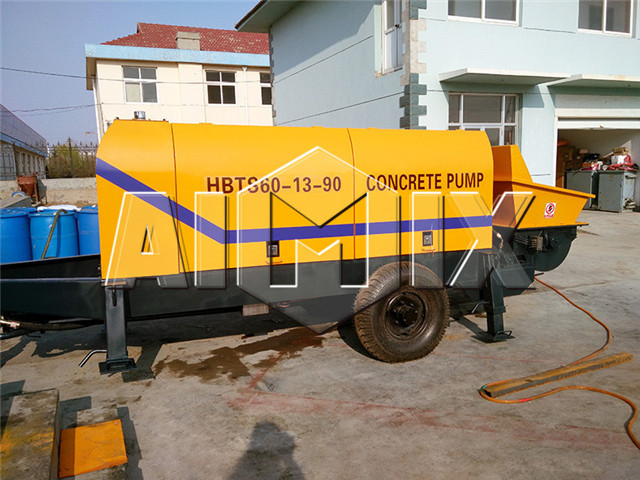
2- Warming the hydraulic oil.
One should regularly warm the hydraulic oil from time to time. This is because of the fact that during the cold days, the oil tends to get thick and at times thicker than molasses.
3- Use anti-freeze liquids and fuel conditioners.
You should ensure that your concrete pump with trailer or concrete mixer pump have brake line anti-freeze liquids and even fuel conditioners at all times. One should also keep the sponge balls in the anti-freeze liquid from time to time as they normally tend to freeze during cold temperatures.
4- Use automatic greasers.
This equipment helps in regularly greasing the concrete pump. It is economical and saves a lot of time hence very effective. One should check the greaser unit from time to time to ensure that the paddle is rotating and turning effectively.
5- How to prevent water from getting into the hydraulic system.
You should make sure that the water box doesn’t get overfilled. One should only let the amount of water in the water box to cover the bottom of the rods hence preventing overflow. One should also regularly drain water from the hydraulic tanks week to week. One should also filter the hydraulic oil monthly.
6- Checking the accumulator bottles and bladders.
One of the hardest working parts of a concrete pump is the accumulator bladder. This means that the nitrogen pressure should be maintained at the required levels. This prevents the bladder from wearing out prematurely.
The best way to check the pressure is by putting the pump into a PTO.
7- Saving the S-tubes.
One should avoid dry stroking the concrete pump especially when there is no even little concrete in the Hooper as this will cause the spline shaft of the S-Tube to wear off prematurely. Make sure you choose a reliable concrete pump company that can save your time and energy on maintenance.